We have complete experience in dryless extrusion granulation production line. We not only focus on every process link in the production process, but also always grasp the process details of each whole production line and smoothly achieve interlinking. The complete production process is one of the main advantages of your cooperation with Yizheng Heavy Industries. We provide customized production line solutions according to the actual needs of customers.
No drying extrusion granulation production line can produce high, medium and low concentration compound fertilizer of various crops. The production line does not need to be dry, with small investment and low energy consumption.
The roller without drying extruding granulation can be designed into particles of different shapes and sizes and can be extruded to produce different sizes.
Compound fertilizer has the characteristics of uniform granulation, bright color, stable quality, and easy dissolution to be absorbed by crops. In particular, it is relatively safe for seeds to grow fertilizer. Suitable for all kinds of soil and wheat, corn, melon and fruit, peanuts, vegetables, beans, flowers, fruit trees and other crops. It is suitable for base fertilizer, fertilizer, fertilizer chase, fertilizer and irrigation.
Raw materials for compound fertilizer production include urea, ammonium chloride, ammonium sulfate, liquid ammonia, ammonium monophosphate, diammonium phosphate, potassium chloride, potassium sulfate, including some clays and other fillers. Various organic materials are added according to soil needs:
1. Animal excrement: chicken, pig's dung, sheep dung, cattle singing, horse manure, rabbit manure, etc.
2. Industrial waste: grapes, vinegar slag, cassava residue, sugar residue, biogas waste, fur residue, etc.
3. Agricultural waste: crop straw, soybean flour, cottonseed powder, etc.
4. Domestic waste: kitchen garbage
5. Sludge: urban sludge, river sludge, filter sludge, etc.
We provide a complete set of dryless extrusion granulation production lines that do not need to be dried. The production line equipment mainly includes mixer, disk feeder, roller extrusion granulation machine, roller sieve machine, belt conveyor, automatic packaging machine and other auxiliary equipment.
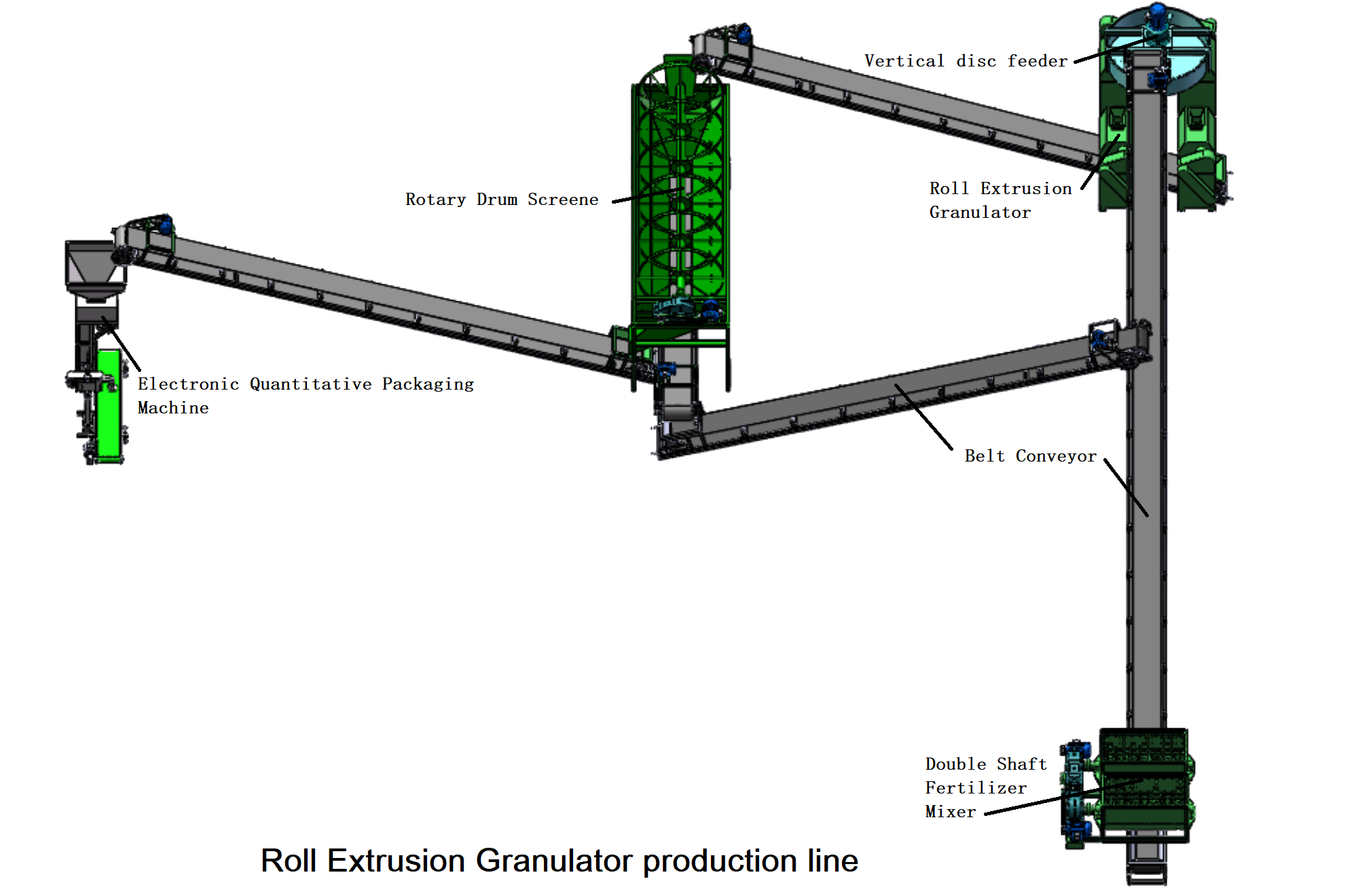
As a professional manufacturer of fertilizer production line equipment, we provide customers with production equipment and the most suitable solution for different production capacity needs such as 10,000 tons per year to 200,000 tons per year.
1. Mechanical pressure granulation is used without heating or humidifying raw materials.
2. Suitable for thermally sensitive raw materials, such as ammonium bicarbonate
3. There is no need to dry the process, with less investment and low energy consumption.
4. No wastewater, exhaust gas emissions, no pollution of the environment.
5. The particle size distribution is uniform, and there is no segregation and agglomeration.
6. Compact layout, advanced technology, stable operation and convenient maintenance.
7. Easy to operate, easy to realize automatic control, and improve production efficiency.
8. There is a wide range of raw material applications without special performance requirements.
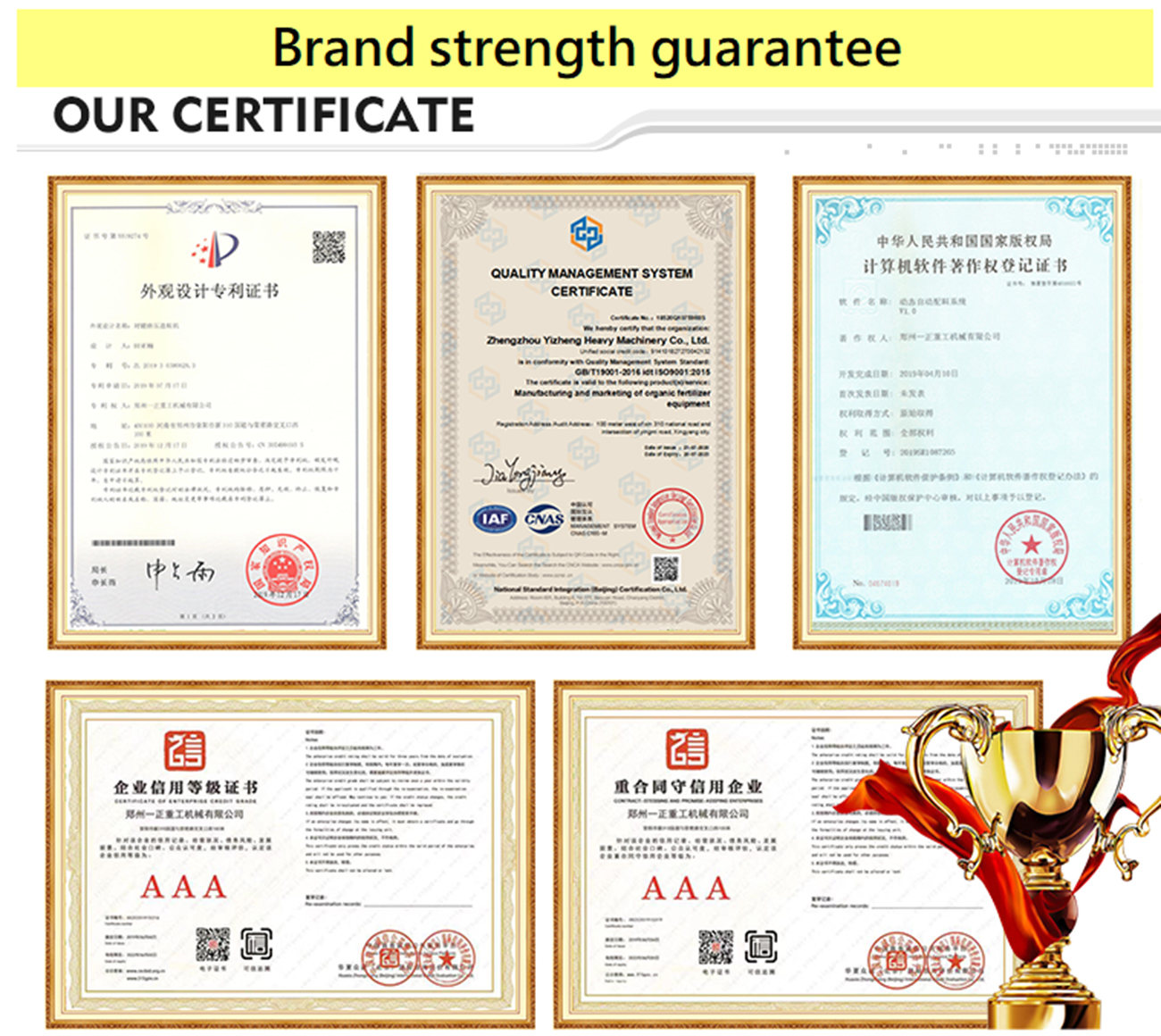
No drying extrusion granulation production line includes automatic batcher, belt conveyor, double-axis blender, disc feeder, extrusion granulation machine, roller screening machine, finished warehouse, automatic packaging machine, etc.
1. Dynamic Batching Machine
The automatic ingredients machine feed the raw materials according to each formula ratio, which can automatically complete the batching process with high accuracy and efficiency, so as to ensure the quality of fertilizer. After the ingredients, the material is transported to the double-axis blender.
2. Double Shaft Fertilizer Mixer
The disc mixer uses a cycloid needle wheel reducer to drive the spindle, and then drive the stirring arm to rotate and stir. With the continuous flip and stirring of the blades on the mixing arm, the raw materials are fully mixed. The mixed material is excreted from the outlet at the bottom. The disk adopts polypropylene plate or stainless steel lining, which is not easy to stick and simple and practical.
3. Roll Extrusion Granulator
The mixed raw material is transported from the belt conveyor to the disc feeder, which evenly sends the material to the four roller extruder under the feeder through the hopper. The machine squeezes the material into pieces to the broken chamber under the roller through a reverse rotating high-voltage roller, and then separates the required particles as the double-axis wolf tooth rod rotates. The roller is made of a new corrosion-resistant, wear-resistant and impact-resistant alloy material.
4. Rotary Drum Screene
Extrified granulation particles are transported to the roller filter through a belt conveyor, and substandard particles flow out of the large particles outlet on the side through the screen hole, and then transported to the disc feeder for secondary granulation, and qualified particles are fed from the lower end outlet and transported to the finished area.
5. Electronic Quantitative Packaging Machine
Through the hopper, qualified particles are weighed quantitatively, and then packaged by an automatic packaging machine.