Groove Type Composting Turner Machine is the most widely used aerobic fermentation machine and compost turning equipment. It includes groove shelf, walking track, power collection device, turning part and transfer device (mainly used for multi-tank work). The working portion of the compost turner machine adopts advanced roller transmission, which can be lifted and non-liftable. The liftable type is mainly used in work scenarios with a turning width of no more than 5 meters and a turning depth of no more than 1.3 meters.
The process design and manufacture of our whole organic fertilizer production line. The production line equipment mainly includes a two-axis mixer, a new organic fertilizer granulator, a roller dryer, a roller cooler, a roller sieve machine, a vertical chain crusher, a belt conveyor, an automatic packaging machine and other auxiliary equipment.
Organic fertilizers can be made of methane residue, agricultural waste, livestock and poultry manure and municipal waste. These organic waste needs to be further processed before they are converted into commercial organic fertilizers of commercial value for sale. The investment in converting waste into wealth is absolutely worthwhile.
Organic fertilizer production line is suitable for:
-- Manufacture of beef dung organic fertilizer
-- Manufacture of cow dung organic fertilizer
-- Manufacture of pig manure organic fertilizer
-- Manufacture of chicken and duck manure organic fertilizer
-- Sheep manure organic fertilizer manufacturing
-- Organic fertilizer manufacturing after municipal sewage waste treatment.。
1. It is used in fermentation and water removal operations in organic fertilizer plants, compound fertilizer plants, sludge waste factories, gardening farms and mushroom plantations.
2. Suitable for aerobic fermentation, it can be used in conjunction with solar fermentation chambers, fermentation tanks and shifters.
3. Products obtained from high-temperature aerobic fermentation can be used for soil improvement, garden greening, landfill cover, etc.
Key Factors to Control Compost Maturity
1. Regulation of carbon-nitrogen ratio (C/N)
The suitable C/N for decomposition of organic matter by general microorganisms is about 25:1.
2. Water control
The water filtration of compost in actual production is generally controlled at 50% ~ 65%.
3. Compost ventilation control
Ventilated oxygen supply is an important factor for the success of compost. It is generally believed that oxygen in the pile is suitable for 8% ~ 18%.
4. Temperature control
Temperature is an important factor affecting the smooth operation of microorganisms of compost. The fermentation temperature of high-temperature compost is 50-65 degrees C, which is the most commonly used method at present.
5. Acid salinity (PH) control
PH is an important factor affecting the growth of microorganisms. PH of the compost mixture should be 6-9.
6. Smelly control
At present, more microorganisms are used to deodorize.
1, Animal manure: chicken manure, pig manure, sheep manure, cow manure, horse manure, rabbit manure, etc.
2. Industrial waste: grapes, vinegar slag, cassava residue, sugar residue, biogas waste, fur residue, etc.
3. Agricultural waste: crop straw, soybean flour, cottonseed powder, etc.
4. Domestic waste: kitchen garbage
5. Sludge: urban sludge, river sludge, filter sludge, etc.
The basic production process of organic fertilizer includes: grinding of raw materials → fermentation → mixing of ingredients (mixing with other organic-inorganic materials, NPK≥4%, organic matter ≥30%) → granulation → packaging. Note: this production line is for reference only.
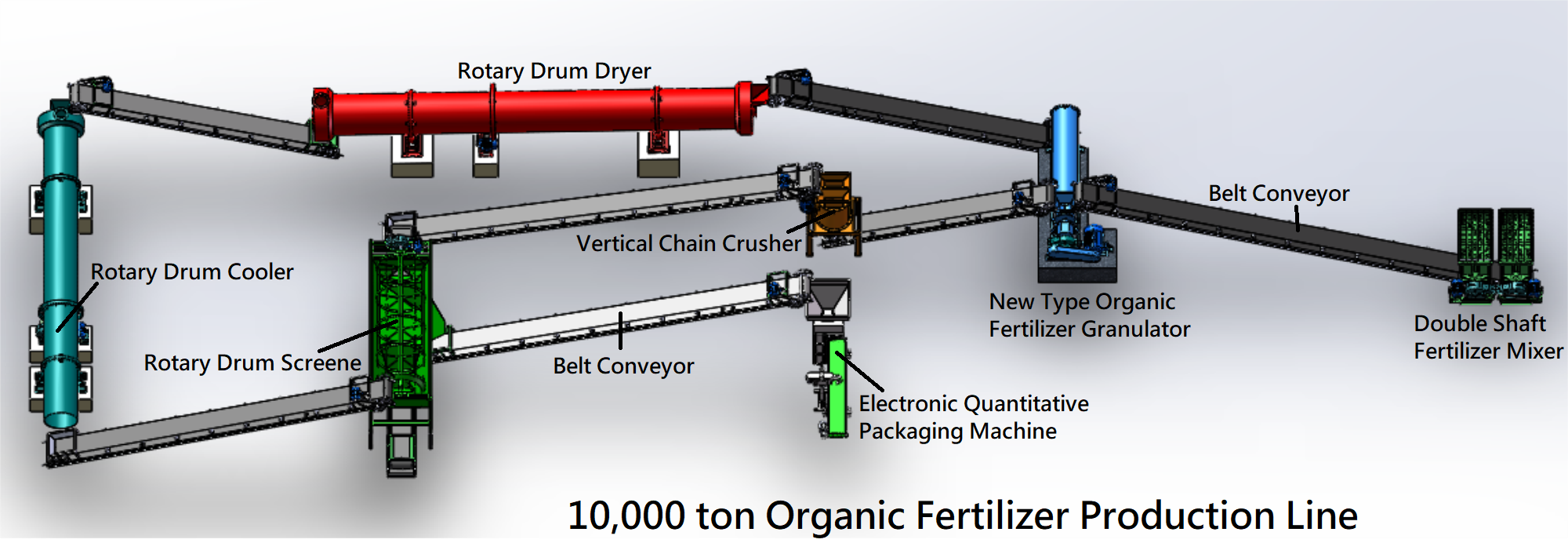
We can not only provide a complete organic fertilizer production line system, but also provide a single equipment in the process according to actual needs.
1. The production line of organic fertilizer adopts advanced production technology, which can complete the production of organic fertilizer at a time.
2. Adopt a patented new special granulator for organic fertilizer, with high granulation rate and high particle strength.
3. The raw materials produced by organic fertilizer can be agricultural waste, livestock and poultry manure and urban domestic waste, and the raw materials are widely adaptable.
4. Stable performance, corrosion resistance, wear resistance, low energy consumption, long service life, convenient maintenance and operation, etc.
5. High efficiency, good economic benefits, little material and regranulator.
6. The production line configuration and output can be adjusted according to customer requirements.
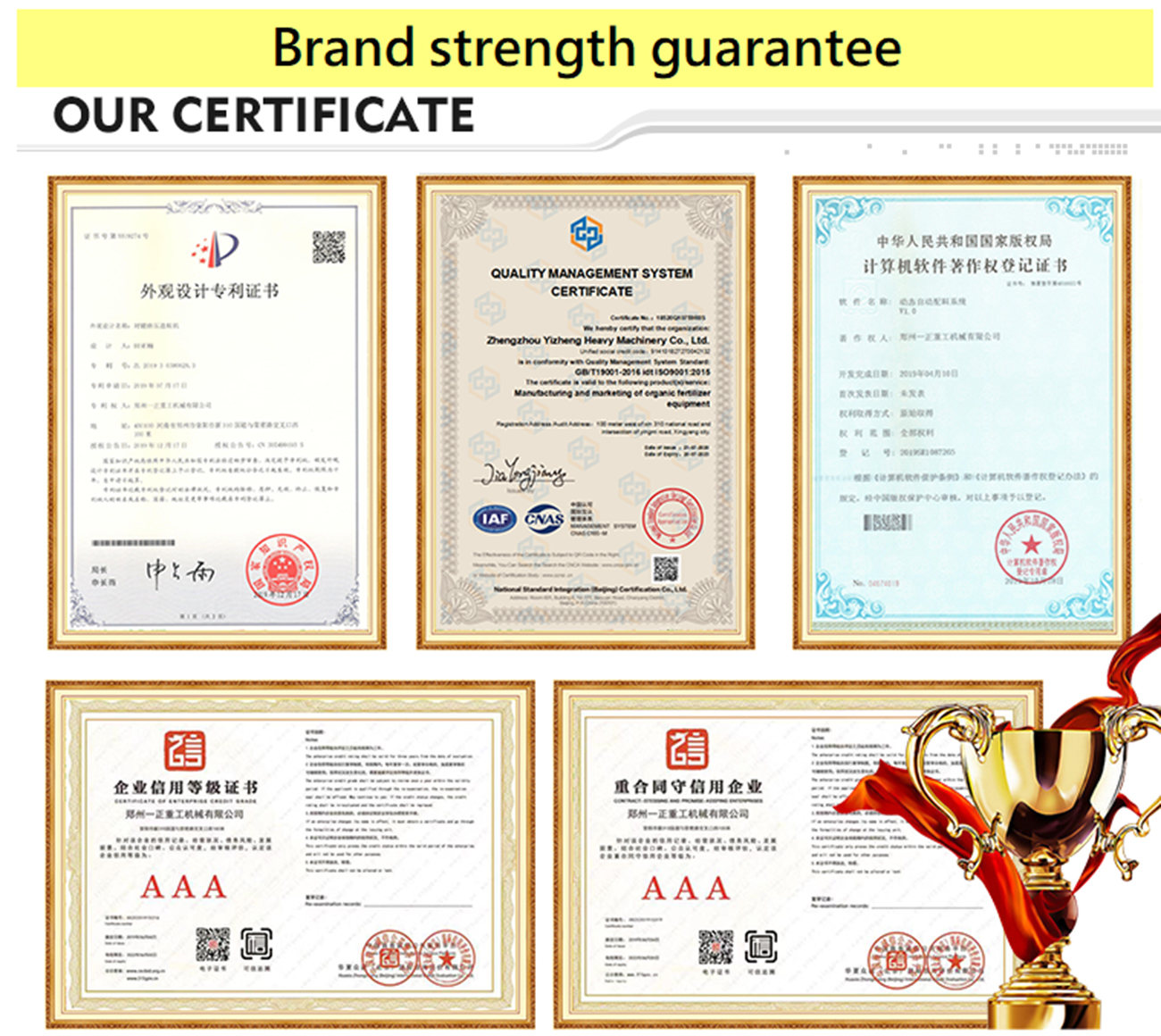
Organic fertilizer production equipment includes fermentation equipment, double-axis mixer, new organic fertilizer granulation machine, roller dryer, drum cooler, drum screening machine, silo, automatic packaging machine, vertical chain crusher, belt conveyor, etc.
Organic fertilizer production process:
1) fermentation process
Drough-type dumper is the most widely used fermentation equipment. The grooved stacker consists of a fermentation tank, walking track, power system, displacement device and multi-lot system. The overturning part is driven by advanced rollers. Hydraulic flipper can rise and drop freely.
2) granulation process
A new type of organic fertilizer granulator is widely used in organic fertilizer granulation. It is a special granulator for raw materials such as animal excrement, decaying fruits, peels, raw vegetables, green fertilizer, sea fertilizer, farm fertilizer, three wastes, microorganisms and other organic waste materials. It has the advantages of high granulation rate, stable operation, durable equipment and long service life, and is an ideal choice for producing organic fertilizer. The housing of this machine adopts seamless pipe, which is more durable and does not deform. Coupled with the safety dock design, the operation of the machine is more stable. The compressive strength of the new organic fertilizer granulator is higher than that of the disk granulator and drum granulator. The particle size can be adjusted according to customer requirements. The granulator is most suitable for direct granulation of organic waste after fermentation, saving the drying process and greatly reducing production costs.
3) drying and cooling process
The particle moisture content after granulation by the granulator is high, so it needs to be dried to meet the water content standard. The dryer is mainly used to dry particles with certain humidity and particle size in the production of organic fertilizer compound fertilizer. The particle temperature after drying is relatively high, and it should be cooled to prevent fertilizer from clumping. The cooler is used for cooling particles after drying and is used in combination with rotary dryer, which can greatly improve cooling efficiency, reduce labor intensity, increase yield, further remove the moisture of particles and reduce fertilizer temperature.
4) screening process
In production, in order to ensure the uniformity of the finished product, the particles should be screened before packaging. Roller sieving machine is a common sieving equipment in the production process of compound fertilizer and organic fertilizer. It is used to separate finished products and non-conforming aggregates and further achieve the classification of finished products.
5) packaging process
After the packaging machine is activated, the gravity feeder starts to operate, loads the material into the weighing hopper, and puts it into a bag through the weighing hopper. When the weight reaches the default value, the gravity feeder stops running. The operator takes away the packaged materials or puts the packaging bag on the belt conveyor to the sewing machine.