The annual production line of 30,000 tons of compound fertilizer is a combination of advanced equipment. Low production cost and high production efficiency. Compound fertilizer production line can be used for granulation of various composite raw materials. Finally, compound fertilizers with different concentrations and formulas can be prepared according to actual needs, effectively replenish the nutrients needed by crops, and solve the contradiction between crop demand and soil supply.
In recent years, the state has formulated and issued a series of preferential policies to support the development of the organic fertilizer industry. The greater the demand for organic food, the more demand there is. Increasing the application of organic fertilizer can not only essentially reduce the use of chemical fertilizers, but also improve crop quality and market competitiveness, and is of great significance for the prevention and control of agricultural non-point source pollution and the promotion of agricultural supply-side structural reform. At this time, aquaculture enterprises have become a trend to make organic fertilizers from excreta, not only requiring environmental protection policies, but also seeking new profit points for sustainable development in the future.
The production capacity of small organic fertilizer production lines varies from 500 kilograms to 1 ton per hour.
Raw materials for compound fertilizer production include urea, ammonium chloride, ammonium sulfate, liquid ammonia, ammonium monophosphate, diammonium phosphate, potassium chloride, potassium sulfate, including some clay and other fillers.
1) Nitrogen fertilizers: ammonium chloride, ammonium sulfate, ammonium thio, urea, calcium nitrate, etc.
2) Potassium fertilizers: potassium sulfate, grass and ash, etc.
3) Phosphorus fertilizers: calcium perphosphate, heavy calcium perphosphate, calcium magnesium and phosphate fertilizer, phosphate ore powder, etc.
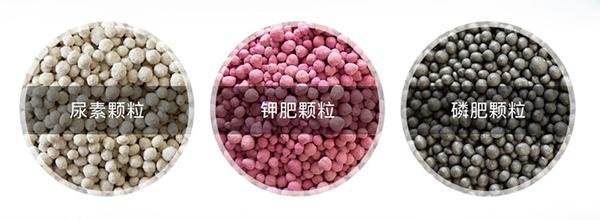
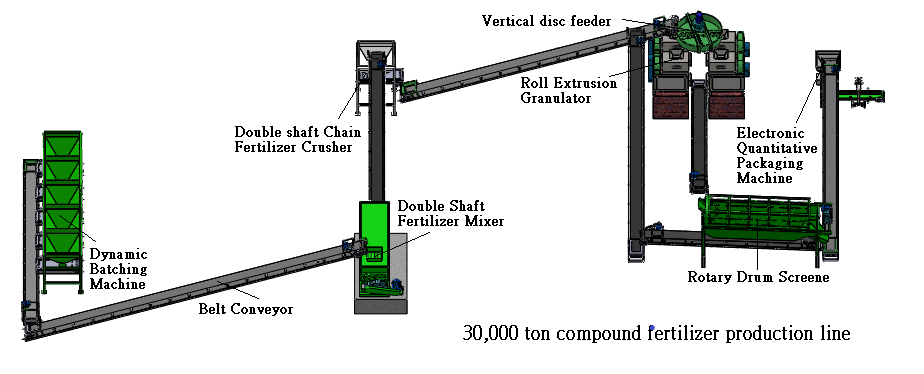
As a professional manufacturer of fertilizer production line equipment, we provide customers with production equipment and the most suitable solutions for different production capacity needs such as 10,000 tons per year to 200,000 tons per year.
1. The raw materials are widely adaptable and suitable for granulation of compound fertilizer, medicine, chemical industry, feed and other raw materials, and the product granulation rate is high.
2. The production risk can produce various concentrations, including organic fertilizer, inorganic fertilizer, biological fertilizer, magnetic fertilizer, etc.) compound fertilizer.
3. Low cost, excellent service. Our factory manufactures and sells by itself as a direct seller to provide maximum customer benefits at the best price. In addition, if customers have technical problems or assembly questions, they can also communicate with us in time.
4. The compound fertilizer produced in this production line has a small moisture absorption volume, is easy to store, and is especially convenient for mechanized application.
5. The whole compound fertilizer production line has accumulated many years of technical experience and production capacity. This is an efficient and low-power compound fertilizer production line that has been innovated, modified and designed, successfully solving the problems of low efficiency and high cost at home and abroad.
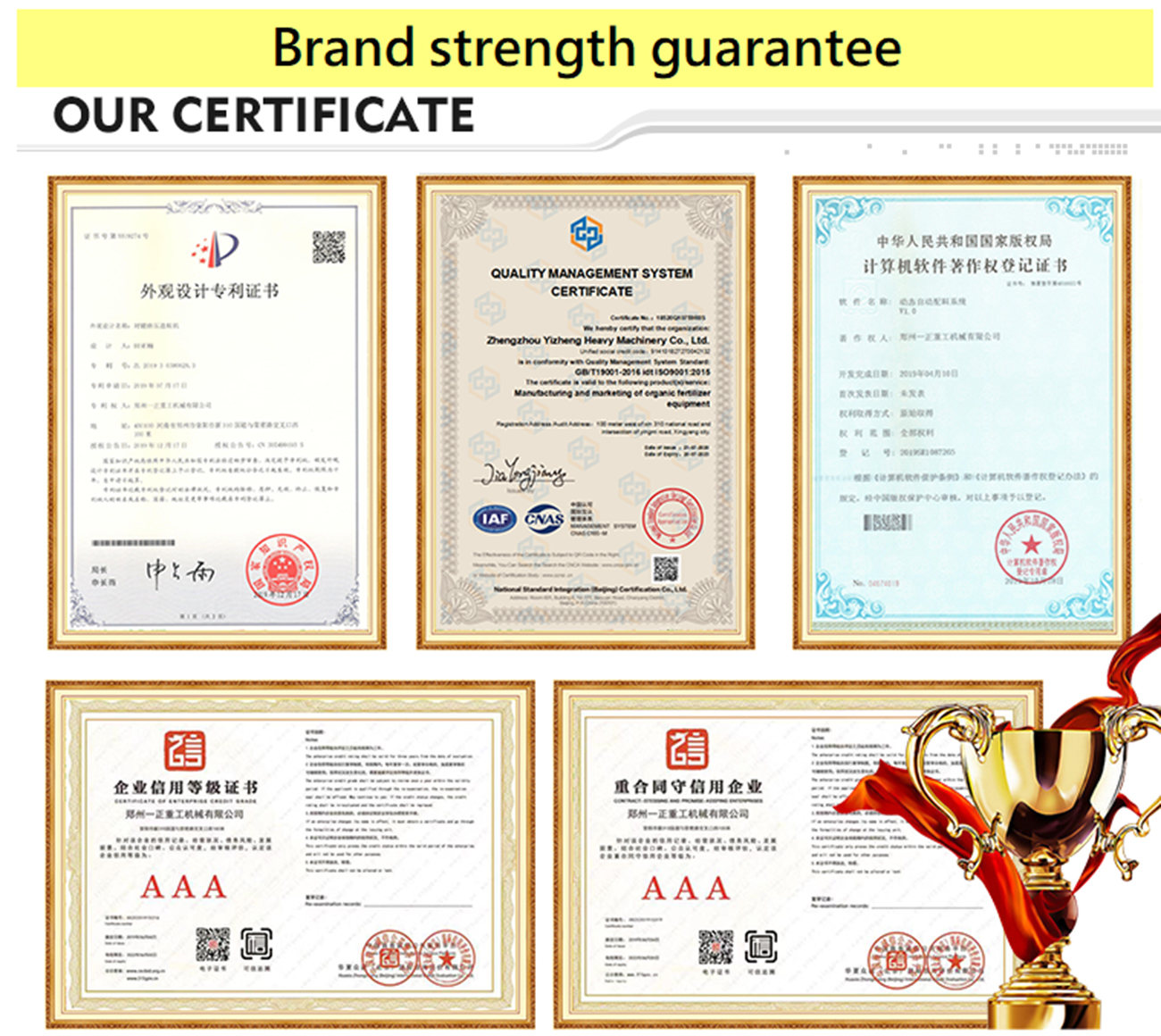
The process flow of the compound fertilizer production line can usually be divided into: raw material ingredients, mixing, granulation, drying, cooling, particle classification, finished coating, and final finished packaging.
1. Raw material ingredients:
According to market demand and local soil determination results, urea, ammonium nitrate, ammonium chloride, ammonium thiophosphate, ammonium phosphate, diammonium phosphate, heavy calcium, potassium chloride (potassium sulfate) and other raw materials are distributed in a certain proportion. Additives and trace elements are used as ingredients in a certain proportion through belt scales. According to the formula ratio, all raw material ingredients are evenly flowed from belts to mixers, a process called premixes. It ensures the accuracy of the formulation and realizes efficient and continuous and efficient ingredients.
2. Mixed raw materials:
Horizontal mixer is an indispensable part of production. It helps the raw materials mix fully again and lays the foundation for high-efficiency and high-quality granular fertilizer. I produce a single-axis horizontal mixer and a double-axis horizontal mixer to choose from.
3. Granulation:
Granulation is the core part of the compound fertilizer production line. The choice of granulator is very important. Our factory produces disk granulator, drum granulator, roller extruder or new compound fertilizer granulator. In this composite fertilizer production line, we choose a rotary drum granulator. After the material is mixed evenly, the belt conveyor is transported to the rotary drum granulation machine to complete granulation.
4. Screening:
After cooling, powdery substances remain in the finished product. All fine and large particles can be screened out with our roller sieve. The screened fine powder is transported from the belt conveyor to the blender to stir the raw material again to make granulation; while large particles that do not meet the particle standard need to be transported to be crushed by a chain crusher before granulation. The finished product will be transported to the compound fertilizer coating machine. This forms a complete production cycle.
5. Packaging:
This process adopts an automatic quantitative packaging machine. The machine is composed of an automatic weighing machine, a conveyor system, a sealing machine, etc. You can also configure hoppers according to customer requirements. It can realize the quantitative packaging of bulk materials such as organic fertilizer and compound fertilizer, and has been widely used in food processing factories and industrial production lines.