To develop green agriculture, we must first solve the problem of soil pollution. Common problems in soil are: soil compaction, imbalance of mineral nutrition ratio, low organic matter content, shallow tillage, soil acidification, soil salinization, soil pollution, etc. To adapt the soil to the growth of crop roots, the physical properties of the soil need to be improved. Improve the organic matter content of the soil, so that there are more pellets and fewer harmful elements in the soil.
We provide the process design and manufacture of a complete set of organic fertilizer production lines. Organic fertilizers can be made of methane residue, agricultural waste, livestock and poultry manure and municipal waste. These organic waste needs to be further processed before they are converted into commercial organic fertilizers of commercial value for sale. The investment in converting waste into wealth is absolutely worth it.
The production line of new organic fertilizer with an annual output of 50,000 tons is widely used in the production of organic fertilizers with agricultural waste, livestock and poultry manure, sludge and urban waste as organic raw materials. The whole production line can not only convert different organic waste into organic fertilizer, but also bring great environmental and economic benefits.
Organic fertilizer production line equipment mainly includes a hopper and feeder, drum granulator, dryer, roller sieve machine, bucket hoist, belt conveyor, packaging machine and other auxiliary equipment.
Widely used raw materials
The new fertilizer production line can be applied to various organic matter, especially straw, liquor residue, bacterial residue, residue oil, livestock and poultry manure and other materials that are not easy to granulate. It can also be used for the treatment of humic acid and sewage sludge.
The following is the classification of raw materials in organic fertilizer production lines:
1. Agricultural waste: straw, bean residue, cotton slag, rice bran, etc.
2. Animal manure: a mixture of poultry manure and animal manure, such as slaughterhouses, waste from fish markets, cattle, pigs, sheep, chickens, ducks, goose, goats' urine and feces.
3. Industrial waste: liquor residue, vinegar residue, cassava residue, sugar residue, furfural residue, etc.
4. Household waste: food waste, roots and leaves of vegetables, etc.
5. Sludge: sludge from rivers, sewers, etc.
The production line of organic fertilizer consists of a dumper, a mixer, a crusher, a granulator, a dryer, a cooler, a packaging machine, etc.

The new organic fertilizer production line has the characteristics of stable performance, high efficiency, convenient maintenance and long service life.
1. This variety is not only suitable for organic fertilizers, but also for biological organic fertilizers that add functional bacteria.
2. The diameter of fertilizer can be adjusted according to the needs of customers. All kinds of fertilizer granulators produced in our factory include: new organic fertilizer granulators, disk granulators, flat mold granulators, drum granulators, etc. Choose different granulators to produce particles of different shapes.
3. Widely used. It can treat different raw materials, such as animal waste, agricultural waste, fermentation waste, etc. All these organic raw materials can be processed into batches of granular commercial organic fertilizers.
4. High automation and high accuracy. The ingredients system and packaging machine are controlled by computers and automated.
5. High quality, stable performance, convenient operation, high automation degree and long service life. We take full account of the user experience when designing and manufacturing fertilizer machines.
Value-added services:
1. Our factory can help provide actual foundation line planning after customer equipment orders are confirmed.
2. The company strictly complies with relevant technical standards.
3. Test according to the relevant regulations of the equipment test.
4. Strict inspection before the product leaves the factory.
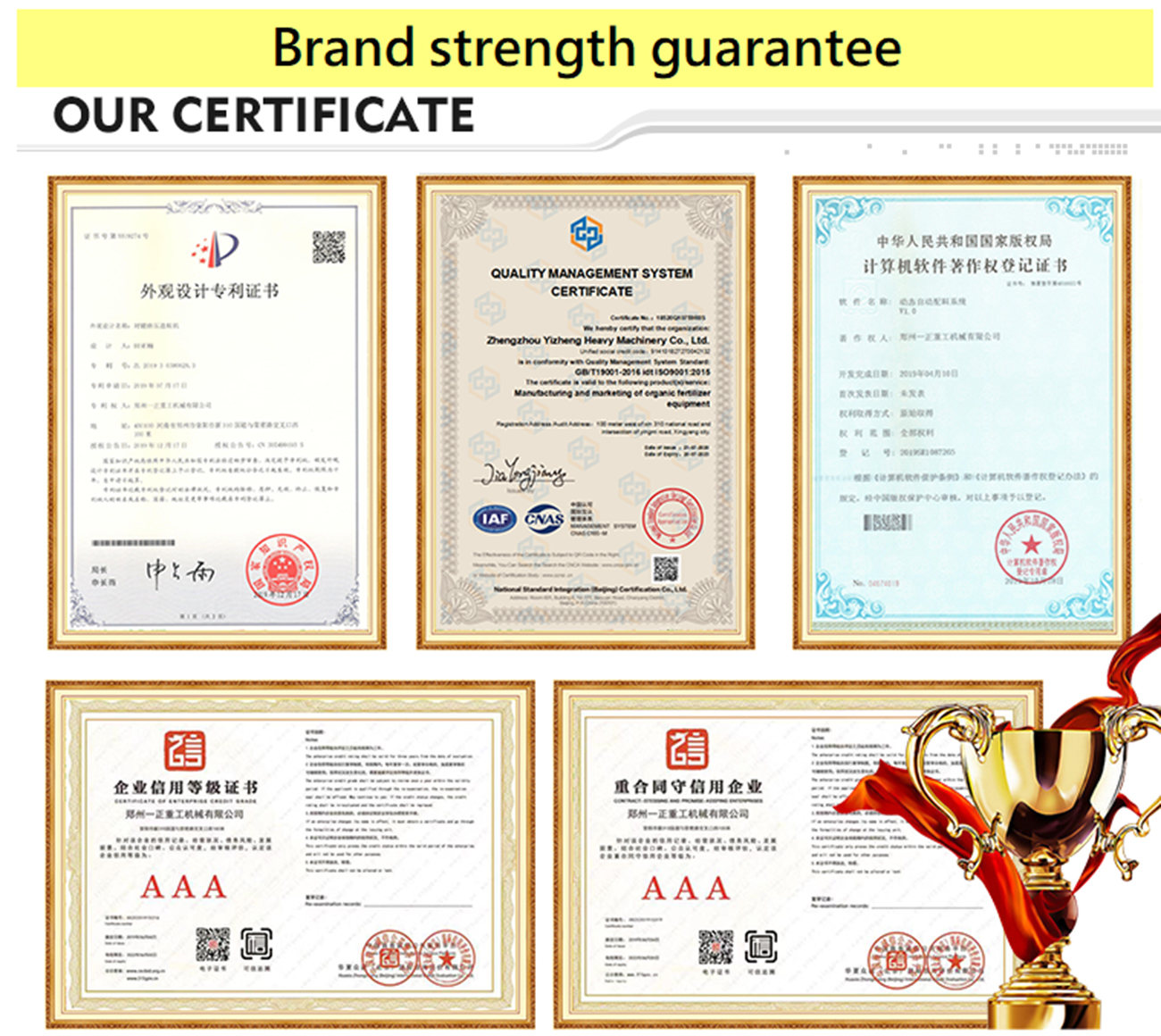
1. Compost
Recycled livestock and poultry excrement and other raw materials are directly entered into the fermentation area. After one fermentation and secondary aging and stacking, the smell of livestock and poultry manure is eliminated. Fermented bacteria can be added at this stage to decompose the coarse fibers in it so that the particle size requirements of the crushing can meet the granularity requirements of granulation production. The temperature of raw materials should be strictly controlled during fermentation to prevent excessive temperature and inhibit the activity of microorganisms and enzymes. Walking flip machines and hydraulic flip machines are widely used in flipping, mixing and accelerating fermentation of stacks.
2. Fertilizer Crusher
The fermented material crushing process that completes the secondary ageing and stacking process can be used by customers to choose a semi-wet material crusher, which adapts to the moisture content of the raw materials in a wide range.
3. Stir
After crushing the raw material, add other nutrients or auxiliary ingredients according to the formula, and use a horizontal or vertical mixer during the stirring process to stir the raw material and additive evenly.
4. Drying
Before granulation, if the moisture of the raw material exceeds 25%, with a certain humidity and particle size, the water should be less than 25% if the drum dryer is used for drying.
5. Granulation
A new organic fertilizer granule machine is used to granulate raw materials into balls to maintain microbial activity. The survival rate of microorganisms using this granulator is more than 90%.
6. Drying
The moisture content of the granulation particles is about 15% to 20%, which generally exceeds the target. It requires drying machines to facilitate the transportation and storage of fertilizer.
7. Cooling
The dryed product enters the cooler through a belt conveyor. The cooler adopts an air-conditioned cooling heat product to fully eliminate residual heat, while further reducing the water content of particles.
8. Sieving
We provide a high-quality and high-performance drum sieving machine to achieve the classification of recycled materials and finished products. The recycled material is returned to the crusher for further processing, and the finished product is delivered to the fertilizer coating machine or directly to the automatic packaging machine.
9. Packaging
The finished product enters the packaging machine through a belt conveyor. Carry out quantitative and automatic packaging of finished products. The packaging machine has a wide quantitative range and high accuracy. It is combined with a conveyor sewing machine with a liftable countertop. One machine is versatile and efficient. Meet the packaging requirements and use environment for different goods.